Why are we doing this?
By Shawn P Quigley and Jon M Quigley
Change Dynamics
Change is a function of tension created by the difference between the current condition and the desired state. It can only occur when this tension contains sufficient energy to overcome external forces. These external forces could be something as simple as the current condition being a habit: habits are established by our brains to allow ease of overall load upon it. When sufficient energy exists to promote the initiation of change action occurs. However, this energy is not infinite and change can become stalled. As with a car that starts any trip, the initial amount of energy expended can be greater than the energy required to continue that trip. However, there is the energy required to complete the trip, and the duration of time required for the change will determine the amount of energy required. For a change, a basic example of the endpoint would be when the new process or procedure has become a habit and it is less likely to reversion to the previous habit or condition.
In the field
Some work is fairly straightforward, there are steps to doing the work that are clear and will remain constant over a period of time. I recall priming tobacco when I was young. A group of, 4 – 6, I do not recall, but essentially one person for each row of tobacco on either side of the area down which the tractor would be driven. Every year was the same until the last year I did the work when the farmer purchased new equipment. The new equipment was not set up to handle the configuration of rows in the field. He had purchased a piece of equipment after he had planted the crop in the field. The equipment was not capable of addressing harvesting the field in its’ current state and would require adjustment if it were to be the sole manner of harvesting. That year, I drove the tractor with the two carts behind, prime (which was pulling select leaves from the plants), and put the tobacco leaves on the cart. By the way, the leaves at the bottom of the plant are called sand lugs, you are practically standing on your head to reach these. I recall there being two rows on either side of the tractor that would require harvesting. As I worked down the rows, I would move the tractor down the center row. The others were sitting on a machine harvesting the leaves and placing them on the conveyor belt that went to the topside of the machine and would then be set up for placing in the new type of barn. While this change did; overall, reduce the time required to harvest the field it is a prime example of how some process improvements are slighted by the lack of foresight. The farmer knew the machine’s design, he also knew he was going to purchase it that year. However, he did not modify his planting routine to allow the maximum effectiveness of his change. While this is a small example, we can apply this to how many other change management processes are employed.
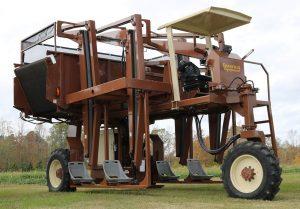
Tobacco Harvester
Photo from https://www.granvilleequipment.com/equipment/harvesters/
Fast food
I worked in fast food for a while and became a manager after a couple of years. I was working at a store in Raleigh and watched the breakfast cooks perform their work. Actually, I liked working in the kitchen, admittedly this is not the same as working in a kitchen of a high-end restaurant, but still required speed and attention to detail, and some memory. There was extra movement, and more steps than required to do the work. Asking why we are doing something, even if the question is only an internal question. I saw how some rewiring and moving of equipment would reduce the work steps without any downside. I went to the backline cook with this proposal, but the main cook did not like the idea. I knew this would work, and I would work the station myself. I do just that. In the end, we moved from batch delivery to single-piece flow (this was in the early 1980s), it saved time, and those working the backline eventually accepted the new configuration. There are two change examples in this story:
- The natural resistance to change without reason: the main cook dismissing the idea without actual evaluation. This natural resistance to change is commonly related to the brain’s desire to make everything a habit. As stated earlier, habitual processes take less effort from the brain and thus allow it to maintain a lower state of energy. Remember newton’s laws: an object at rest tends to stay at rest until acted upon by an external force. This also applies to our brain.
- Change implementation to provide a direct indication of process or procedural improvement. When the manager took the time to set up the change and prove out the process it allowed the workers to see both the potential for improvement and the dedication of management to improving the conditions in which they work.
Professional Experience
Local
Much later in my career, I spent some time as a process manager. I had worked in a few of the departments of this organization, as well as many years prior to this experience. I worked with the groups, not just the managers of the groups, to understand the flow of the work, beyond what I had experienced through work.
We reviewed each of the steps, especially the exchanges between the various groups. Each output from one group, that would go to another group was quantified. The result was a clearly defined expectation of the work produced by the “customer.” Coming to a common understanding of the flow of the work, developing a common lexicon, and an agreement on what are the attributes of work products that one department would deliver to another.
We then documented each of these steps, beginning with the why. For example, for each step, the first item in the outline was the objective. Why are we doing this? How would we know we have successfully delivered? Additionally, in our experience, we may find that the description of the process cannot be enacted exactly as articulated. A well-articulated objective can help the team members decide if perhaps this objective does not apply to this project, or in those cases where we are unable to achieve the objective by means of this process, we can then explore alternative solutions for how to achieve it.
Clickable link
Global
Another interesting experience, perhaps, is from a global company. This company had a number of sites across the world. Each of these sites was staffed differently, that is the volume of talent available in the central site was greater than the other sites, most notably the North American site. There was a push to use one set of processes, while not having the same structure and tools, similar staffing, and available talent, and generally having different advantages. Proposing a global process in the face of differing organizational advantages and disadvantages is essentially a one size fits all approach. This is more dogmatic than a sound philosophical approach (what you value, and limits to how you will respond or trade-off limits) to the work based upon conditions in which the work is performed. Arbitrary change based upon one dynamic is flawed in inception. While it is advantageous to have a common process or procedure throughout an organization, it is not always practical based on the differing structures. Analysis of change should not be only from the organization at large but also departmental.
Summary
In general, at least for product development work, we will be learning about the important portions of the product and even how to get to the end product. There may be principles, product and quality management sort of things, that you may prioritize above some other attributes. There is no single way to do the work, best practices are circumstances and situational depending.