Cost Management
For an enterprise to thrive costs must be under control. There are many approaches of varying complexity available to ensure the organization’s costs are optimized. The variety of techniques allows any organization, independent of levels of complexity and sophistication to critique the cost structure and explore alternatives throughout the product lifecycle.
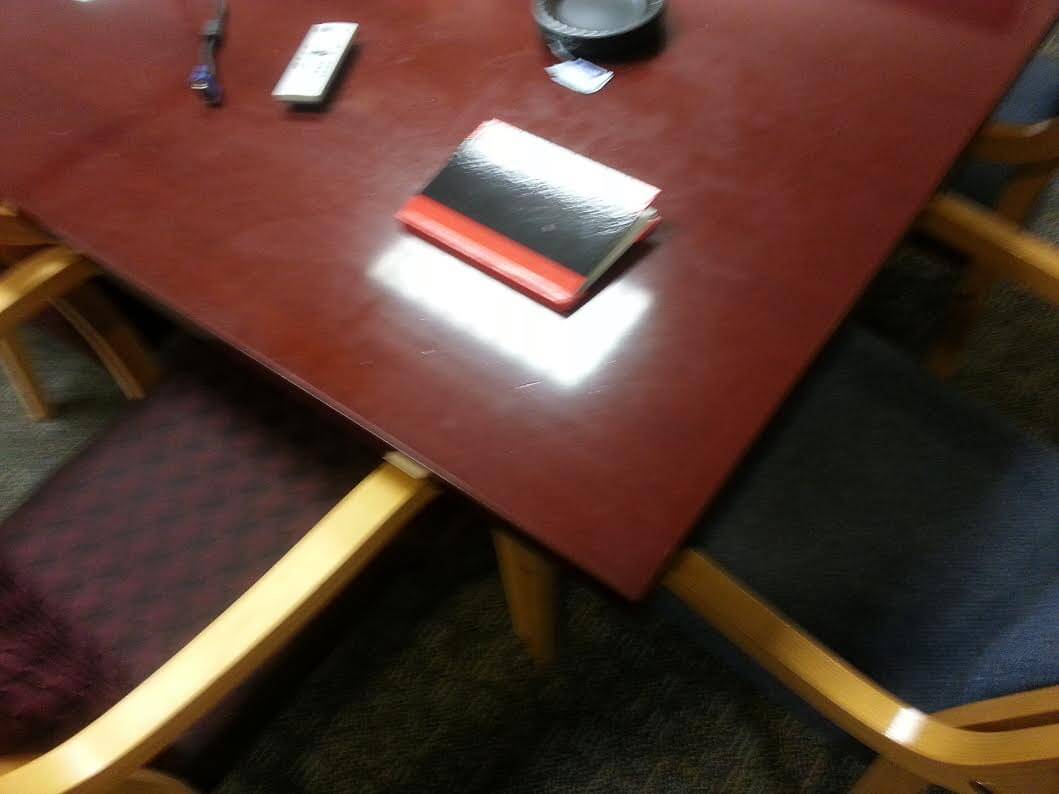
Brainstorming
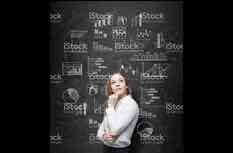
Brainstorming can be used for problem-solving as well as uncovering alternative approaches that may improve the cost structure for the product or process. Brainstorming is conducted multidiscipline to gather the most perspectives possible from which selection of the best possible solution will be made. We will employ many team idea generating and collecting methods as well as the use of tools such as mind mapping to build associations from which we can generate the best solution. Brainstorming does not apply solely to cost, but can also be applied to design solutions as well. We have used this technique many times to improve cost and generate intellectual property (patents).
Function Allocation Systems Technique
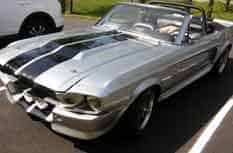
FAST is an acronym for functional analysis system technique. FAST allows us to reduce ambiguity in the definition of a functional product or a functional process. Value of a product is interpreted differently by different customers. Characteristics that are common to value are high level performance, capability, emotional appeal, and style relative to its cost. Value is generally expressed in terms of maximizing the function.
Value = (Performance + Capability)/Cost
Value = Function/Cost
Lean
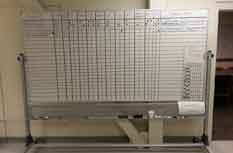
Lean is a set of techniques that are typically employed to improve the costs in manufacturing by reducing waste, but not exclusively. In fact, this technique can be applied to process management in general, such as product development, and not just manufacturing. Cost improvement comes from managing and controlling aspects of manufacturing that have increase the cost. This includes transportation, inventory, motion, wait, over processing, over production, and defects.
Make or Buy Analysis

Make or buy analysis considers the scope and objective of the work compared to the company strategies and tactics for growth. Make refers to the company decision to internally handle the design and or fabrication of the component or subassembly. Buy refers to outsourcing the component or subassembly. There can be many compelling reasons to select one or the other of these alternatives rather than leave to random chance or little forethought.
Teardown
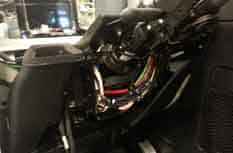
Teardowns are used to learn the cost implications of the design, often another manufacturer of the product. Tearing the product down is one method to identify and understand the cost drivers for the product. This includes the manufacturing, material composition and assembly of the product. The teardown will be multidiscipline approach to obtain a multitude of perspectives that will help ascertain the constituents of the product cost. This can be material, design or methods of production.
Building a Cause and Effect Diagram
Pugh Matrix
How to Brainstorm
Using Pareto Charts